Михаил Нижник, генеральный директор, ООО «Группа МЕТТАТРОН»
Александр Черный, технолог, ООО «Группа МЕТТАТРОН»
В первой и второй частях мы рассмотрели состав паяльных паст, влияние составляющих на конечный результат, а также факторы, определяющие качество печати. В продолжении цикла обратимся к термическим характеристикам паст и особенностям
ТЕРМОПРОФИЛЬ
Рассмотрим состояние и поведение паяльной пасты во время процесса оплавления (рис. 32).
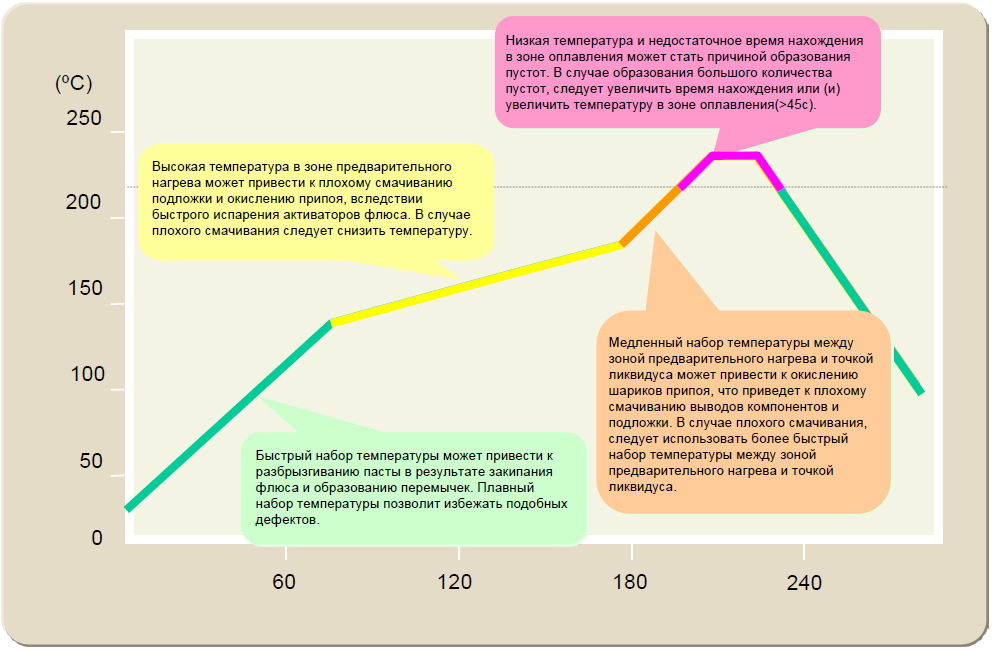
Рис. 32. Обзор зон термопрофиля
Начальный набор температуры
При повышении температуры растворители начинают испаряться. Характер испарения определяется индивидуальными температурами испарения используемых во флюсе растворителей. Смолы и тиксотропные материалы начинают размягчаться. Характер размягчения зависит от температур размягчения отдельных компонентов, лежащих в диапазоне 100–140°С.
Быстрый набор температуры может привести к разбрызгиванию пасты в результате закипания флюса и образованию перемычек. Плавный набор температуры позволит избежать подобных дефектов.
Стадия предварительного нагрева
На этой стадии растворители должны полностью улетучиться из пасты. Происходит активация флюса и равномерное распределение тепла в подложке.
Флюс становится очень мягким, переходит в жидкое состояние, равномерно обволакивает частицы припоя, растекается по подложке и защищает частицы припоя от повторного окисления.
Одновременно с повышением температуры и плавлением компонентов флюса «включаются» канифоли и активаторы, которые удаляют пленку окиси с частиц порошка припоя и с подложки.
Высокая температура в зоне предварительного нагрева может привести к плохому смачиванию подложки и окислению припоя вследствие быстрого испарения активаторов флюса. В случае плохого смачивания следует снизить температуру.
Если температура выводов компонентов растет быстрее, чем прогревается вся площадка, то слишком короткая зона предварительного нагрева приведет к тому, что при расплавлении припоя он переместится на выводы. В месте пайки выводов соберется излишнее количество припоя, который контактирует с соседними выводами. Поэтому если перемычки припоя возникают на этой стадии процесса, то необходимо провести регулировку зоны предварительного нагрева.
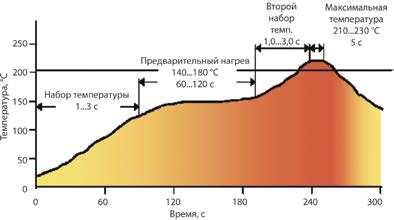
Рис. 33. «Седлообразный» профиль нагрева
Второй набор температуры
Когда частицы припоя достигают температуры плавления (точки ликвидуса), припой расплавляется, реагирует с флюсом, очищается от окисей, и происходит пайка.
Для большинства паяльных паст рекомендуемое время нахождения припоя в расплавленном состоянии составляет 30–40 с, чтобы обеспечить полное плавление припоя и достаточное время на смачивание спаиваемых поверхностей в случае, если в изделии установлены весьма теплоемкие компоненты.
Медленный набор температуры между зоной предварительного нагрева и точкой ликвидуса может привести к окислению шариков припоя, что приведет к плохому смачиванию выводов компонентов и подложки. В случае плохого смачивания, следует использовать более быстрый набор температуры между зоной предварительного нагрева и точкой ликвидуса.
Низкая температура и недостаточное время нахождения в зоне оплавления может стать причиной образования пустот. В случае образования большого количества пустот, следует увеличить время нахождения или (и) увеличить температуру в зоне оплавления (> 45 с).
ТИПЫ ТЕРМОПРОФИЛЯ
В конвекционных печах оплавления используются два профиля нагрева: линейный и седлообразный (см. рис. 33). Хотя рекомендуется работать по показанному на рисунке 32 седлообразному профилю, давайте посмотрим, что стоит за каждым из этих подходов.
Когда пайка оплавлением только начала внедряться в технологию поверхностного монтажа, количество компонентов на поверхности изделия было не очень большим, и разница в теплоемкости отдельных элементов была незначительной. Простая конфигурация платы позволяла без особых проблем работать с плавным набором температуры, без зоны предварительного прогрева.
Миниатюризация привела к повышению плотности монтажа и к появлению весьма теплоемких элементов типа корпусов BGA и QFP.
Большой разброс теплоемкости отдельных компонентов не давал добиться теплового равновесия при нагреве по линейному закону (и даже по седлообразному), да еще в обычных инфракрасных печах с проблемами затенения и разницы теплопоглощения
Тогда появился процесс пайки оплавлением в паровой фазе, который позволял добиться весьма хорошей равномерности прогрева. Однако от него вскоре пришлось отказаться
Затем появился популярный сейчас процесс пайки в конвекционных печах, который обеспечивает гораздо более равномерный прогрев, чем инфракрасные печи.
Что касается причины, по которой в нем используется седлообразная кривая нагрева, то она заключается в стремлении добиться с помощью принудительной циркуляции такого же теплового равновесия, которое было характерно для процесса пайки в паровой фазе.
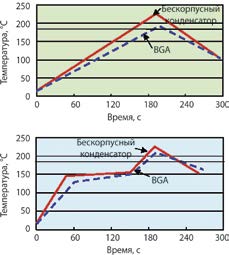
Рис. 34. Прогрев компонентов разной
величины при линейном и
седлообразном температурном профиле
При разработке кривой нагрева более важно учитывать характер и конструкцию электронных компонентов и подложки, нежели поведение паяльной пасты в ходе нагрева. Пример: измерим температуру пайки бескорпусного конденсатора и микросхемы в корпусе BGA (см. рис. 34). Разница в теплоемкости влияет на скорость прогрева и температуру.
При седлообразном термопрофиле пайки компоненты с большей теплоемкостью догоняют по температуре остальные компоненты до начала следующего участка набора температуры. Это уменьшает разницу температур компонентов в точке пайки.
На рисунке 35 показана разница в поведении вязкости паст при линейном и седлообразном термопрофиле. Более резкий набор температур в седлообразном профиле обуславливает необходимость использования большего количества типов растворителей с разной температурой кипения.
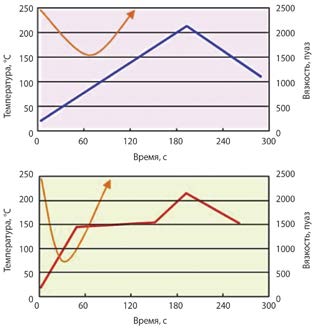
Рис. 35. Изменение вязкости пасты
при линейном и седлообразном профиле нагрева
Работать можно и с линейным, и с седлообразным профилем, лишь бы передавалось количество тепла, необходимое для испарения растворителей. При настройке термопрофиля нужно тщательно учесть все аспекты, влияющие на равномерный нагрев всех поверхностей (как компонентов, так и печатной платы), чтобы обеспечить качественную пайку каждого компонента.
Исходя из опыта технологов, работающих на производстве, можно сказать, что неверно выбранный размер и форма апертур гораздо сильнее влияют на качество пайки и появление дефектов (перемычек и бусинок припоя), чем не совсем корректно подобранный термопрофиль.
Оценка надежности готовых изделий
При использовании безотмывочных паст после пайки на поверхности печатной платы остается некоторое количество остатков флюса. Требуемый уровень надежности определяется заказчиком в зависимости от характера изделий. В соответствии с международным стандартом IPC, электронные изделия делятся на три класса:
Class 1 — изделия общего назначения. Для них допустимо некоторое количество дефектов, и критерии надежности к ним предъявляются минимальные. Пример: компьютерная мышь.
Class 2 — изделия, нарушение функционала которых чревато последствиями. Это бытовая техника, электроника в автомобилях. Например, телевизор при выгорании печатной платы может вызвать пожар.
Class 3 — изделия, от бесперебойной работы которых зависит здоровье и жизнь людей. Это системы жизнеобеспечения, авиастроение. Зачастую в третьем классе изделий выделяются подклассы, которые можно условно назвать «Military» и «Space». Class 3C — газоанализатор в угольной шахте; Class 3B — военная техника; Class 3A — система жизнеобеспечения на МКС.
Как говорилось в первой статье цикла, паяемость и надежность зачастую антагонистичны, поскольку все активаторы (органические кислоты, галогены) коррозионно агрессивны и могут снизить надежность в зависимости от их содержания в остатках флюса.
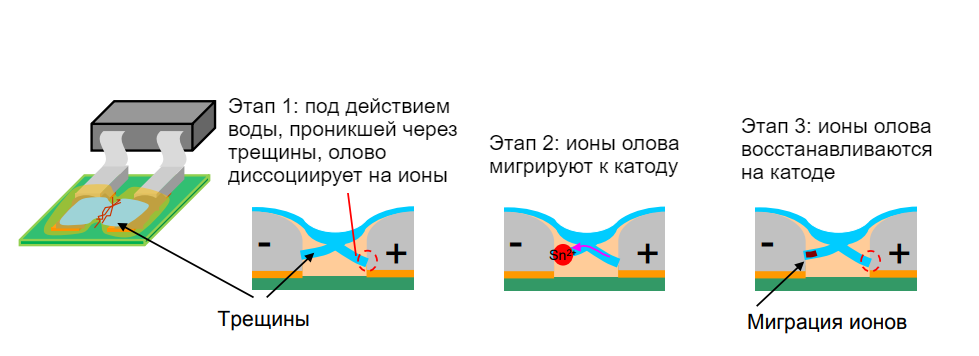
Рис. 36. Механизм возникновения ионной миграции
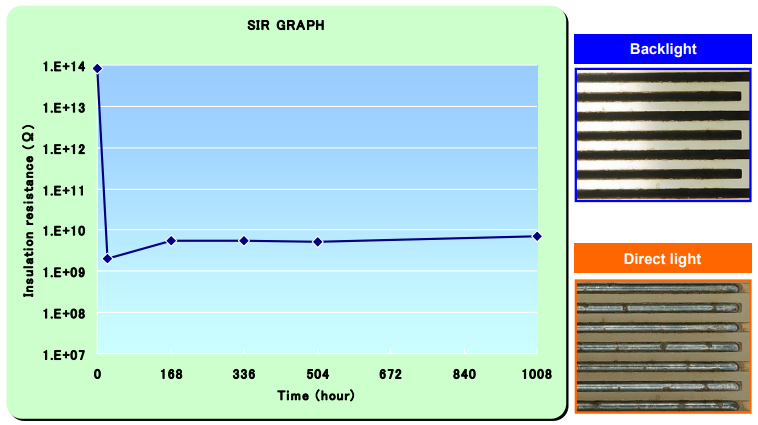
Рис. 37. Пример диаграммы SIR
При проверке надежности продукта проверяют следующие показатели:
— Проверка деградации электроизоляционных свойств пасты (см. рис. 36, 37 и 38). Это испытание характеризует флюс по степени снижения сопротивления изоляции жесткого гребеночного электрода в условиях высокой влажности и температуры. Флюс испытывают на поверхностное сопротивление по методике
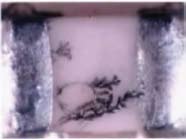
Рис. 38. Дендриты
Компания «KOKI», кроме классических методов, применяет собственные, более жесткие испытания.
— Коррозия. Для испытания флюса на коррозионную агрессивность (см. рис. 39) применяют два метода: тест на коррозию медной пластины и медного зеркала. В зависимости от применяемых стандартов (IPC, JIS
— Ионные загрязнения. Это испытание оговаривается в стандарте MIL. При погружении оплавленной платы в водный раствор изопропилового спирта на ионографе по сопротивлению определяют количество ионных остатков. Полученную величину сопротивления пересчитывают в NaCl (г/см2). Уровень ионных остатков, допустимый по МIL для паст с флюсом RMA, не должен превышать 3,1 г/см2. Однако, поскольку этот тест определяет ионное загрязнение, вызванное не только флюсом, но и подложкой и компонентами, то получаемые результаты используют только для справки.
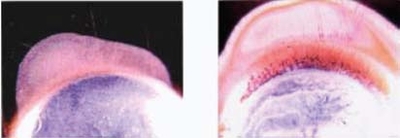
Рис. 39. Тест на коррозионную стойкость
Остатки флюса
Флюс паяльной пасты состоит из растворителей и твердых веществ: смол, активаторов, тиксотропных материалов. Содержание твердых веществ во флюсах паяльных паст «KOKI» составляет до 60–70%, причем большая часть этих веществ после пайки остается на поверхности изделия в виде остатка.
Поскольку столь большое количество твердых веществ поддерживает заданные реологические и другие свойства пасты, то понятно, что, не прибегая к пайке в среде азота, снизить их содержание технически трудно.
При разработке новых флюсов производители стремятся к тому, чтобы смолы во флюсе были по возможности бесцветными — это улучшает косметический вид платы после пайки.
Контролепригодность изделий
По мере миниатюризации электронных компонентов и роста плотности монтажа становится все труднее разместить на плате необходимые контрольные точки для проверки цепей. Поскольку при отсутствии таких площадок щупы тестера контактируют непосредственно с галтелью припоя, состояние и расположение остатков флюса на месте пайки становится важным фактором тестируемости схемы.
Типичные факторы, затрудняющие контакт щупа с металлом, и меры преодоления проблем приводятся в таблице 5.
Факторы | Меры преодоления |
---|---|
Объемный остаток флюса | Поскольку толстый осадок снижает проводимость и ухудшает контакт щупа, следует, насколько это возможно, снизить содержание твердых веществ |
Растекаемость флюса | Как и в приведенном выше случае, для лучшего контакта желательно иметь по возможности более тонкий слой остатков флюса. Флюс следует составлять так, чтобы во время пайки он обтекал кромку припоя и оставлял на нем как можно более тонкий слой осадка |
Твердость остатка | При ударе пробника по остатку флюса он растрескивается, и его кусочки прилипают к носику щупа, что ухудшает электропроводность. Поэтому нужно подбирать компоненты флюса так, чтобы его остатки сохраняли определенную пластичность |
Конструкция тестера (тип щупа, контактное давление, местоположение контакта и т.д.) | Использование одноштырьковых пробников, увеличение давления при контакте и т.д. |
Однако реализовать хорошую тестируемость по приведенным рекомендациям на практике проблематично, и вот почему:
— Уменьшение количества твердых составляющих флюса отрицательно скажется на других характеристиках пасты, таких как печатаемость, срок жизни, клейкость, паяемость.
— Растекание флюса можно регулировать использованием смол, канифолей и тиксотропных материалов с низкой температурой плавления. Например, температура плавления канифоли марки WW («прозрачная, как вода») составляет всего 80°С, но ее применение в композиции флюса вызывает серьезные проблемы с осадкой пасты.
— Твердость остатков флюса. Подобно растекаемости, твердость остатков флюса теоретически можно регулировать с помощью легкоплавких смол. На деле же для стойкости к осадке приходится вводить смолы с более высокой температурой размягчения, например смолы, полимеризованные абиетиновой кислотой. Такие смолы размягчаются при температуре порядка 140°С, и
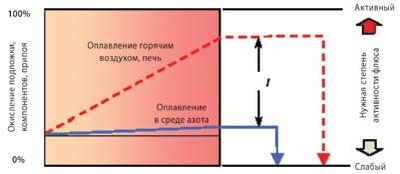
Рис. 40. Окисление в воздушной среде и в среде азота
ОСОБЕННОСТИ ПАЙКИ ОПЛАВЛЕНИЕМ В СРЕДЕ АЗОТА
Паяльные пасты с размером зерна менее 10 мкм сильно окисляются при нагреве в атмосферном воздухе, потому что отношение площади поверхности частицы припоя к ее объему обратно пропорционально радиусу частицы, а толщина окисной пленки не зависит от размера частицы. Чем мельче размер зерна, тем большее количество металла окислится.
Для предотвращения повторного окисления паяльной пасты в процессе оплавления применяется пайка в среде азота. В конвекционную печь оплавления подается не атмосферный воздух, а практически чистый азот с содержанием кислорода < 1000 ppm.
Достоинства пайки в среде азота:
— улучшается паяемость;
— уменьшается количество остатков флюса;
— можно паять очень мелкие элементы;
— повышается надежность.
Улучшение паяемости
Нет необходимости поддерживать химическую активность флюса на протяжении процесса пайки, поэтому основное внимание уделяется смачиваемости и вязкости.
Уменьшение количества остатков флюса
В отличии от пайки в атмосфере, при пайке в азотной среде нет необходимости вводить в состав флюса большое количество канифолей, так как не происходит повторное окисление. Поэтому остатков флюса после пайки будет на порядок меньше.
Надежность
Нет необходимости вводить большое количество активаторов, поэтому намного увеличивается поверхностное сопротивления остатков флюса, и флюс обладает самой низкой химической активностью.
Единственный недостаток пайки в азотной среде — дороговизна оборудования. Поэтому следует внимательно изучить и обосновать необходимость использования этого специального процесса: возможно, требуемую надежность можно получить и в воздушной атмосфере, оптимизируя разводку платы, состав пасты и режим пайки.
ПАЙКА КОМПОНЕНТОВ СО ШТЫРЕВЫМИ ВЫВОДАМИ (THT-монтаж)
В большинстве случаев на печатную плату монтируются как
Альтернатива —
— нанесение паяльной пасты на контактные площадки;
— установка
— установка компонентов со штыревыми выводами;
— пайка в печи оплавления.
При необходимости двустороннего монтажа последовательность операций будет такой:
— нанесение паяльной пасты на контактные площадки;
— нанесение термоотверждаемого клея под корпуса наиболее тяжелых элементов;
— установка
— переворачивание платы;
— нанесение паяльной пасты на контактные площадки и в сквозные отверстия;
— установка
— установка компонентов со штыревыми выводами;
— пайка в печи оплавления.
Такой порядок монтажа используется при производстве большинства миниатюрных устройств, таких как смартфоны и ноутбуки.
Ключевой вопрос при внедрении такого процесса: как обеспечить нанесение нужного количества пасты (припоя) в отверстия.
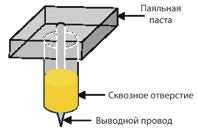
Рис. 41. К расчету количества пасты для нанесения в отверстия
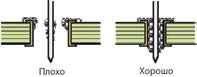
Рис. 42. Если вывод слишком тонок, припоя может не хватить для нормальной пайки в отверстие
Паяльная паста — смесь припоя и флюса в отношении 1:1 по объему. Необходимое количество паяльной пасты вычисляют по объему сквозного отверстия и площади сечения вывода (см. рис. 41). Чтобы обеспечить необходимое количество припоя, учитывайте следующее.
Конструкция подложки
Шаг между отверстиями определяет размер и форму апертур. Проблемы возникают при малом шаге между отверстиями. Слишком маленький шаг осложняет
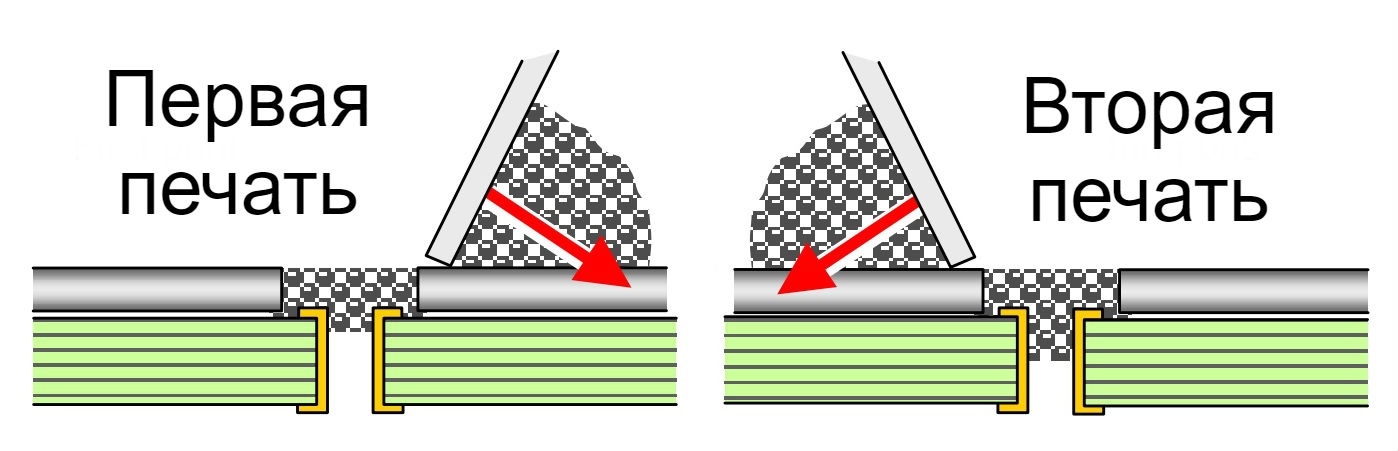
Рис. 43. Печать в два прохода
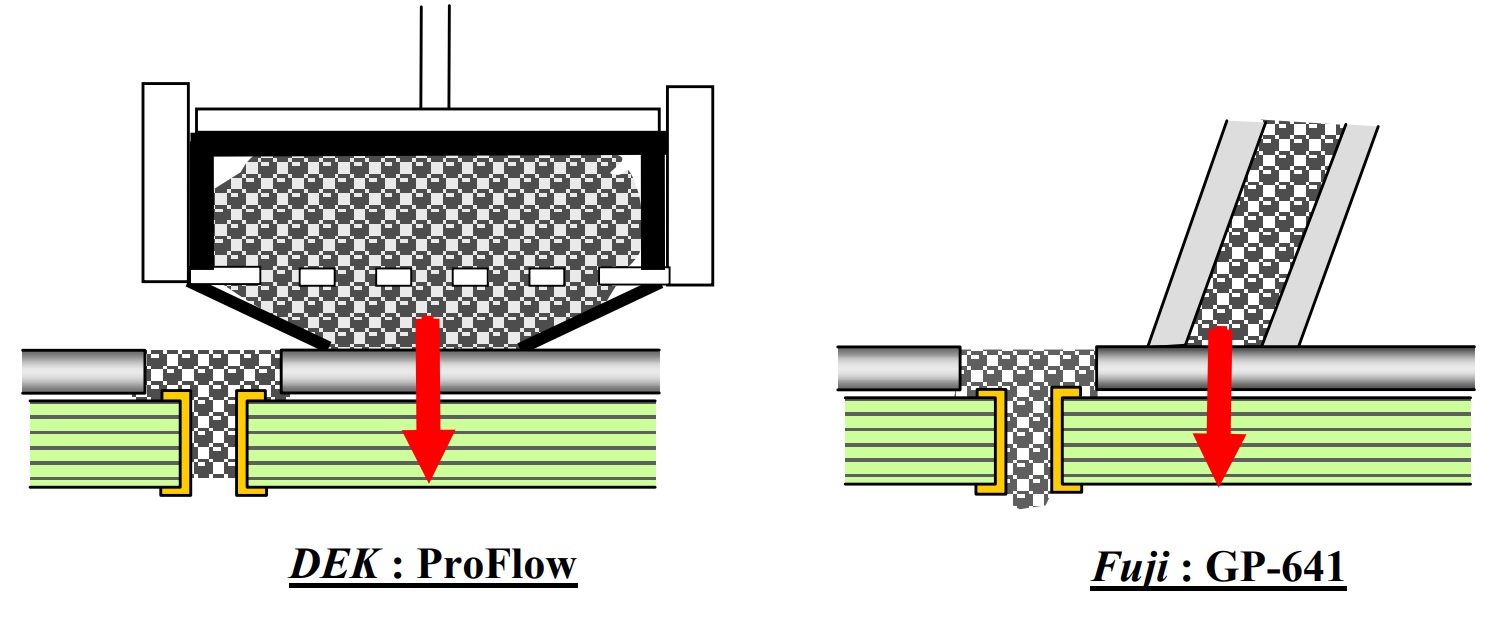
Рис. 44. Печать на вертикальном прессе
Диаметр отверстия
Если диаметр отверстия значительно превосходит диаметр вывода, то при передвижении печатной платы по конвейерной линии и установке компонента паяльная паста может выпасть из отверстия (см. рис. 42).
Метод печати и модель принтера также влияют на нанесение достаточного количества припоя.
Обычная печать с металлическим или резиновым ракелем (в два прохода)
Чтобы обеспечить нанесение достаточного количества пасты, необходимо нанести ее не только на поверхность контактной площадки, но и в каждое сквозное отверстие. При традиционной печати необходимо сделать, по крайней мере, два прохода (см. рис. 43), чтобы некоторое количество пасты попало в отверстия. Однако такая многозаходная печать может привести к размазыванию пасты и образованию перемычек при высокой плотности печатного рисунка.
Нанесение паяльной пасты при помощи дозатора
Можно выделить два типа нанесения паяльной пасты при помощи дозаторов: контактное и бесконтактное. При контактном нанесении паяльной пасты используется трафарет. Принцип нанесения схож с нанесением при помощи ракеля: поршень выдавливает пасту из кассеты через печатающую головку, которая перемещается по поверхности трафарета. В печатающую головку паяльная паста подается под постоянным давлением, поэтому паста заполняет все апертуры и сквозные отверстия.
При бесконтактном нанесении паяльная паста наносится непосредственно на каждую контактную площадку и в каждое переходное отверстие по отдельности, и объем наносимой паяльной пасты определяется временем нанесения.
Трафареты
На количество пасты, попадающее в отверстие, сильно влияют следующие характеристики трафарета:
— Толщина трафарета. Стандартный вариант: 100 мкм. Увеличение толщины трафарета определенно помогает увеличить количество наносимой в отверстие пасты без роста площади отпечатка. Например, при увеличении толщины трафарета со 100 до 150 мкм прирост по объему составляет 50%. Допустим, флюс и припой в пасте смешаны в объемном соотношении 1:1. Это значит, что увеличение толщины трафарета на 50 мкм дает увеличение количества наносимого припоя на 25%.
— Габаритные размеры апертур. Учитывайте диаметр металлизированного отверстия и размеры вывода компонента.
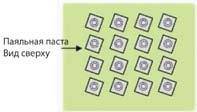
Рис. 45. Нанесение паяльной
пасты для разъема PGA
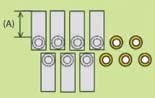
Рис. 46. Нанесение паяльной
пасты для штекерного разъема
Конструкция апертур
В зависимости от конструкции компонентов, шаг между сквозными отверстиями может быть очень маленьким. В таких случаях потребуется прибегать к особой конструкции апертур. Пример для разъема адаптера PGA показан на рисунке 45; для штекерного разъема — на рисунке 46.
Длину, А и ширину определяйте с учетом минимально необходимого объема припоя и опасности возникновения перемычек с соседними площадками.
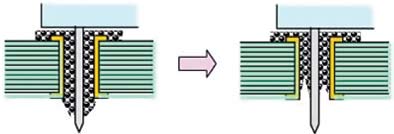
Рис. 47. Вытеснение пасты из отверстий выводом
Паяльная паста
Паста, применяемая для процесса
Вязкость
— На стадии печати: при использовании стандартных принтеров с ракелем лучше использовать пасты с низкой вязкостью. Менее вязкие пасты легче проникают в отверстия. При использовании контактных дозаторов лучше работать с пастами более высокой вязкости, поскольку при увеличении вертикального давления, что требуется для увеличения количества пасты, загоняемого в отверстие, на схемах с высокой плотностью печатного рисунка паста подтекает под трафарет. Для дозаторов с бесконтактным нанесением выпускаются специальные паяльные пасты.
— При передвижении печатной платы по конвейерной линии и установке компонентов: на рисунке 47 слева вывод компонента заходит в заполненное пастой отверстие. Если вязкость пасты слишком низка, при тряске на скоростном координатном столике во время автоматического монтажа компонентов
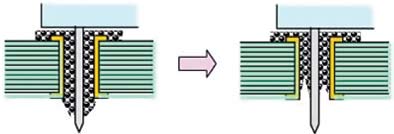
Рис. 48. Контроль изделия после пайки методом «штырек в пасте»
Контролепригодность
При
Еще раз отметим, что при внедрении процесса
В зависимости от метода, который используется на Вашем производстве, компания «KOKI» поставит Вам паяльную пасту, максимально подходящую под Ваш технологический процесс.
Советуем прочитать:
Паяльные пасты: Все о главном. Часть 1
Паяльные пасты: Все о главном. Часть 2